Between Revolution and Digital Transformation: What is Industry 4.0?
For several years now, we’ve been hearing about Industry 4.0 and the revolution it brings to production. But what exactly is Industry 4.0?
Defining Industry 4.0
Industry 4.0 represents the fourth industrial revolution, referring to the integration of digital technologies into production processes and value chains. This era is an evolution of digitalization, impacting all sectors to varying degrees. It is characterized by the extensive use of the Internet of Things (IoT), Artificial Intelligence (AI), Big Data, advanced automation, and predictive analytics. Together, these technologies are transforming not only how products are manufactured but also how companies organize themselves and manage information flows.
The Origins of Industry 4.0
The concept of Industry 4.0 was first introduced in Germany at the Hanover Fair in 2011 as part of a strategy to enhance the competitiveness of manufacturing in an increasingly globalized and competitive market. Unlike previous industrial revolutions—focused on mechanization, electrification, and computerization—Industry 4.0 is marked by a deep fusion of the physical and digital worlds. Production tools and machinery are now operated and controlled by digital technologies and software, embedding digital capabilities into reality.
Goals of Industry 4.0
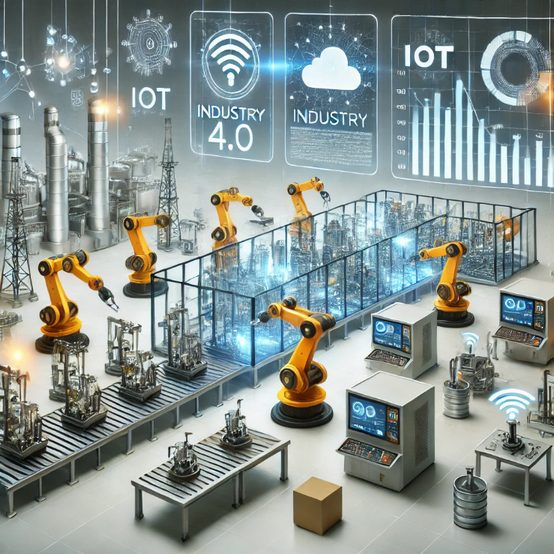
The primary objective is to make factories smarter through interconnected machines, sensors, and production systems. This interconnectedness enables faster, more precise, and autonomous decision-making. Intelligent automation helps companies optimize processes, reduce production costs, improve product quality, and respond faster to market demands.
Key Technologies in Industry 4.0
- Internet of Things (IoT): IoT connects machines and equipment into a network, enabling real-time data exchange for remote monitoring, predictive maintenance, and optimized production processes.
- Big Data and Advanced Analytics: Data from sensors and machines is analyzed to identify trends, anticipate failures, and customize products based on customer needs. This robust data exploitation enables informed decisions at every stage of production.
- Artificial Intelligence (AI) and Machine Learning: AI systems learn from data to continuously improve performance and make autonomous decisions. For example, AI can automatically adjust production parameters to maximize efficiency and minimize waste.
- Advanced Robotics: Next-generation robots, often equipped with learning capabilities, can collaborate with humans or other robots to perform complex tasks with high precision. Their flexibility allows quick adaptation to production changes, enhancing factory agility.
- Additive Manufacturing (3D Printing): This technology builds objects layer by layer from digital files, eliminating the need for molds or specific tooling. It enables mass customization and more decentralized production.
Benefits and Challenges of Industry 4.0
Benefits:
- Productivity Gains: Smart factories produce more in less time, reducing human errors and unexpected downtime through predictive maintenance.
- Enhanced Customization: Flexible systems meet specific customer demands with shorter and more agile production cycles.
- Energy Efficiency and Sustainability: Optimized processes reduce energy consumption and waste, contributing to more sustainable production.
Challenges:
- Data Security: The increasing interconnectivity of systems exposes companies to higher cybersecurity risks. Robust measures are essential for the security of data.
- Investment Costs: Transitioning to Industry 4.0 requires significant investment in equipment and employee training.
- Change Management: Companies must adapt their operations and help employees embrace new skills and technologies.
Impact on Engineering and Production
In the coming years, Industry 4.0 will profoundly reshape engineering and production:
- Engineering: Collaboration will become more virtual with digital twins—virtual replicas of production systems used for real-time testing and optimization. This will enable the development of more complex products with shorter design times.
- Production: Automation and flexibility will dominate. Manufacturing lines will adjust automatically to demand changes or product customization, while real-time data utilization will optimize operations, enhance product quality, and lower costs and environmental impact.
To succeed, engineers must upskill in technologies like AI, IoT, and data analytics to maintain competitiveness.
How to Prepare for Industry 4.0
The transition requires investments in equipment, technology, and workforce training. Businesses need to:
- Assess their maturity in Industry 4.0.
- Define clear strategies for integrating technologies.
- Ensure robust cybersecurity to protect interconnected systems.
- Foster a culture of innovation and adaptability.
SESAHUB offers solutions to support your Industry 4.0 transformation, enabling businesses to achieve smarter, more connected production systems.
Key Takeaways
Industry 4.0 is more than a set of innovative technologies—it’s a new paradigm for manufacturing. By connecting machines, data, and processes, it radically transforms how goods are produced and distributed. While not all companies are at the same maturity level for Industry 4.0, those that seize its opportunities can achieve significant gains in competitiveness, responsiveness, and sustainability. However, success depends on overcoming challenges such as technological innovation, cybersecurity, and workforce training.
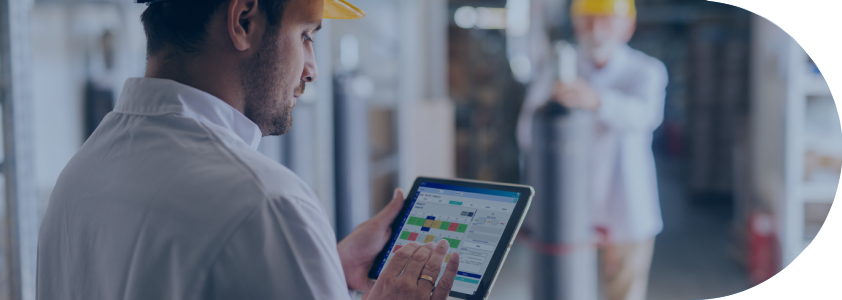
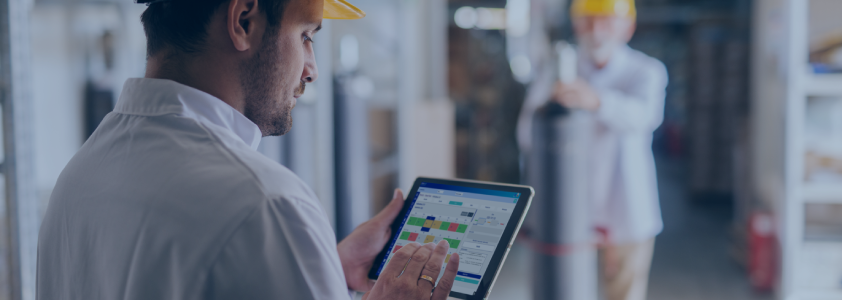