How to achieve a successful digital transformation?
5 tips for a successful digital transformation!
In the digital age, companies must adapt to the challenges of digital transformation regardless of their sector of activity. New technologies are an asset for the organization, they bring an improvement of service, tool, work for all the actors of the company.
This transition is applied in the world and the digitalization is constantly renewed. It is necessary for any business to implement all the digital tools to improve its services and its internal organization.
Digital transformation is constantly evolving and represents a turning point in the company’s evolution. Successfully sharing the company’s strategy with a strong involvement of its managers and deploying it dynamically throughout its organization is a key challenge for management.
Digital transformation is not only about being present on the internet, reviewing your marketing strategy or your communication on social networks. It is a change that involves the entire company organization as well as its internal functioning process.
Indeed, all departments of companies are concerned, and it is essential to implement digital tools within organizations for all uses.
What is the purpose of a digital transformation?
It is a transition in the operating processes of a company. The aim is always to improve its products and services for customers. However, it is not unimportant to improve its internal organisation, as well as the analysis methods that allow the adjustment of action plans. Digital tools allow for more automation in all departments for all uses (data collection in the production centre: TPM, use of data in marketing – sales).
The setting of precise objectives makes it possible to closely monitor the progress of internal improvement and thus its effectiveness. The impact of the implementation of these technologies is on the quality of service and product to the customer, but also on the integration and improvement of new working conditions.
This can be shown by the removal of time-consuming tasks that allow the implementation of new actions and changes that ensure better productivity.
How to set the digital transformation in motion?
The setting of tasks that can be improved or replaced by any digital support is very important. The action plan therefore already allows for a digital improvement strategy to be put in place.
To ensure that this transformation is carried out properly and that the strategy and objectives are monitored, it is necessary to link the actions to indicators. If the communication system put in place makes it possible to communicate the missions, values, objectives, means, and methods implemented, it is important to give meaning to the company’s employees, such as the results in real time. All employees, whatever their level in the company’s hierarchy, will be integrated into this transition and will be able to act, evaluate or react according to the results obtained in a continuous improvement process.
For this, Digital Visual Management is essential for smooth and simple communication and digitalisation. Information must be visible, readable, and understandable to everyone. Digital Visual Management develops internal communication and data broadcasting. The aim is simple, to increase the efficiency of the company from the organisation to the customer. This online management is a good example of how change can be made internally through digital transformation and aims to collect data to improve internal services, management, organisation, and processes.
Industry 4.0 tools help in the gathering of field data (digital data). Thanks to these sources of information shared in real time, it is easier to implement corrective actions and solutions. This communication method is based on the principles of LEAN Management.
To do this, SESA SYSTEMS assists you throughout your digital transformation.
What are the steps and challenges in digital transformation?
Adopt the software designed for real-time information gathering and indicator display.
The SESA HUB software is designed for your employees and can be used by everyone. This real-time information sharing generates performance indicators that can be consulted in a glance. This improves the efficiency of the company and makes it much more reactive thanks to digital visual management. It applies to all organizations.
Off-roader mobility for everyone!
Employees choose which media to work with and have access to specific choices within the range of products that can be taken care of by IT. Online access to the corporate network is instantaneous.
The supports make it possible to be more productive. Being mobile is a priority, especially during a Gemba Walk. To make your LEAN processes more efficient, SESAHUB is compatible with all screens. The software works on a phone, a tablet, or a computer. Thus, you will be able to collect information more easily, wherever you are and, in a few clicks, using your cell phone.
Time saving for your meetings and follow-up of goals.
Your meetings will be based on up-to-date, real-time data. No more multiple data entry! Access figures, performance indicators, plan applications, schedules, and agendas in one place. Everything is centralised to facilitate your tasks. The meeting is over. Write a summary directly in the platform to communicate with your employees about the actions to come. All you need is an internet connection to access all these tools.
Remove unnecessary tasks with our simple and intuitive tool. Optimise your action plans with SESA SYSTEMS Digital solutions that ensure their implementation. These tools allow you to improve the entire customer experience and the internal organisation of your company.
SESA SYSTEMS supports you in your digital transformation thanks to the “Industry 4.0” product range, which includes connected screens such as the E-LEANBOARD, which can be used to display indicators, as part of a Visual Management approach. Other products such as the E-MEETING are used to analyse the company’s key indicators and to share information.
In addition to the physical products, we also offer software solutions such as SESAHUB, which allows you to control the company by connecting the different screens to this software. We also offer a software solution for production with SESA MES.
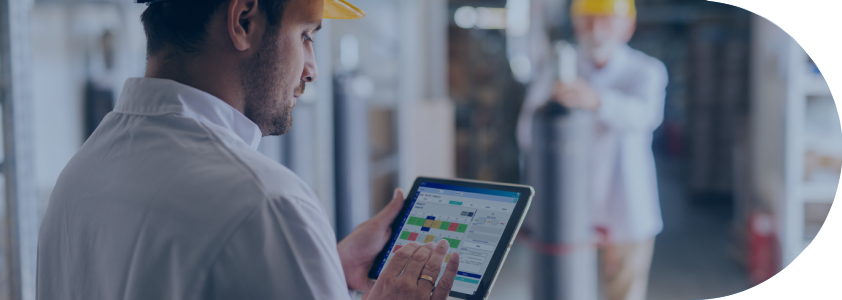
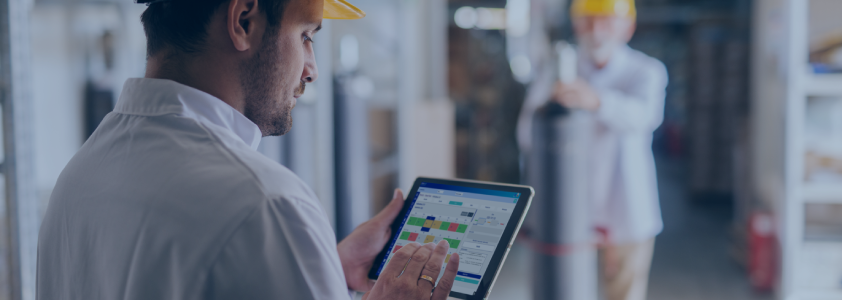