How to manage your digital indicators in 4 steps
Good management is based on actions with recent and up-to-date data. Indeed, without having a quantified value of the impact, it is difficult to take measures. Feedback on actions taken is essential for management. But how can you get this type of information in real time? By setting up indicators and more particularly digital indicators.
What is a key performance indicator?
A KPI, Key Performance Indicator, is a numerical data that helps in decision making. This indicator provides an evaluation of a strategic situation to check whether or not the objectives have been achieved. There are many indicators, it is up to you to determine them. All sectors are concerned, including the industrial sector.
To be effective and to pilot an activity correctly, the performance indicators must be regularly updated. Indeed, if the data is too old, it is no longer realistic, and the actions undertaken will be less effective. This is why it is possible to analyse these indicators in several ways: weekly, monthly, quarterly, or even annually.
Performance management through vision
A performance management approach must be visual. Why? Because visual management is a very effective way of increasing the performance of your company and your employees. Indeed, this type of management is based on visual communication. But it must be done well to prove its effectiveness.
The aim of visual management is to provide information in a few seconds. At a glance, it is possible to know where the situation stands. To implement this type of management, it is possible to use whiteboards. However, this system does not provide real-time data. Thus, performance indicators will not be up to date, a lot of time will be wasted and KPIs will become obsolete quickly. MUDAs should be eliminated from the start in a Lean approach. Digital visual management can solve these failures.
Digitalisation of key performance indicators
Digital transformation brings many benefits to the teams. When operators carry out their daily tasks, the digital visual management guides them. With the help of up-to-date data, errors are reduced. This permanent access to information allows decisions to be taken more quickly and the company’s capacities to be increased to the maximum. The digitalisation of key performance indicators therefore brings several benefits to the company. This type of management is called digital visual management and is part of an Operational Excellence approach. Thanks to digitalization, the whole company improves continuously and faster. The integration of Industry 4.0 is for everyone, regardless of the size of your company.
Steps to manage your KPIs.
STEP 1 – Identify your issues.
First, it is important to put the ideas down. This means hierarchising the problems that visual management will be able to solve. This practice helps to know where the company wants to go.
STEP 2 – Set your goals.
Step 2 consists of finding the most appropriate solution to set up an efficient and coherent visual management system according to your problems and goals. This procedure must be carried out with all employees, which is one of the principles of the Lean culture. Indeed, digital visual management is built with the help of KPIs, i.e. actions are defined according to the results achieved or to be achieved. Thanks to this vision, it is easier to find solutions to existing problems. This is why, in order to have as many different points of view as possible, it is necessary for all employees in the field to participate in this process.
STEP 3 – Analyse your indicators.
The most important thing in this type of approach is the analysis. Collecting data is one thing, using it is another. It is this use that will enable all the benefits of digital visual management. Analysing your indicators means knowing whether the objectives previously set have been achieved. This is why it is essential to set up KPIs that measure the evolution of your actions. For example, it is possible to establish indicators based on production performance, but also on the ergonomics of operators or on the increase in employee skills.
STEP 4 – Time to start.
Now that you know the steps to take, all that remains is to implement them. In order to help you, we have created a management software that links your specifications and the implementation of performance indicators on your screens: SESAHUB. It is a dashboard on which you can find your digital indicators and carry out various corrective actions following this.
If you would like to discuss this with one of our experts, please contact our account managers or request a demonstration of the platform. They will be delighted to support you in your continuous improvement project through visual management.
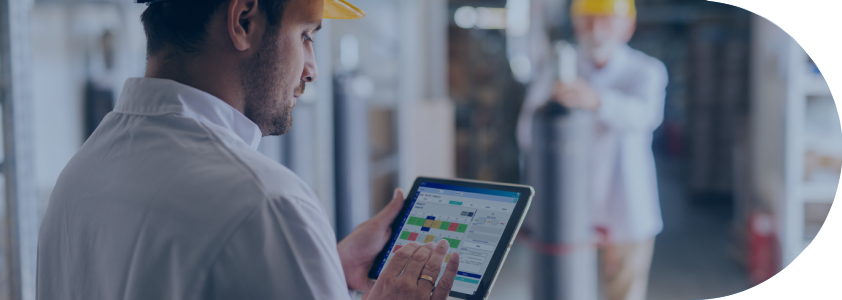
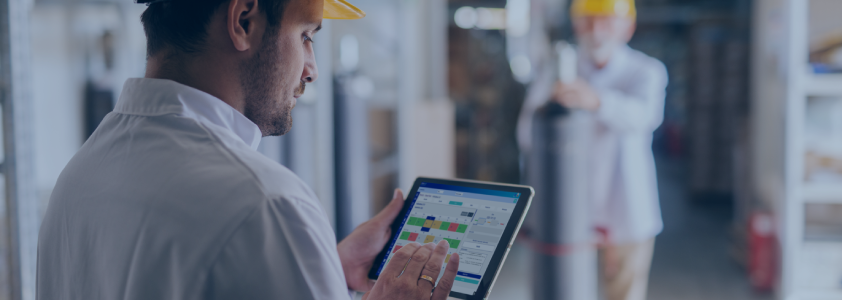