How to update digital indicators in the industry?
What is an indicator?
In business, we talk about KPIs (Key Performance Indicators).
What are the KPI’s?
These indicators are a tool to obtain a clear picture of the company’s business performance. To be more efficient, companies will therefore rely on the results obtained by these previously selected indicators. These results allow companies to set SMART objectives.
There is a wide range of KPIs, and the choice of these indicators must be made according to the sector of activity and the company’s goals.
What are the most important types of KPIs?
There are four main types of key performance indicators:
- Productivity performance indicators:
Here, it is the relationship between the produced results and the resources used for the production. With these indicators, it is possible to analyse the synthetic efficiency rate (SER) of the machines or the running rate.
- Quality performance indicators:
These are the standards for the products and services offered that are studied.
The analysis of these indicators can be done with the compliant products rate, the defective products rate…
- Capacity performance indicators
These indicators help companies to determine the maximum quantity of products and services that can be created.
Here, we will analyse the rate of stock turnover, the rate of stoppages due to shortages, etc.
- Strategic performance indicators
They allow companies to establish long-term strategies.
We will analyse the feasibility of the objectives set… for example.
These performance indicators are present in all areas of activity but here we will focus on the industry sector.
What criteria should the different KPIs meet?
To know if the chosen indicators are relevant, they must meet 5 criteria. To check the relevance of the chosen KPIs, the SMART tool is used:
- S It must be specific and express an objective clearly
- M It must be measurable and quantifiable
- A It must be achievable and have accessible goals.
- R It must be realistic
- T It must be temporal and therefore limited in time
KPIs allow the company to stick to its goals, to develop and monitor a strategy, indicators are necessary for the performance of the company.
Digitalising the various KPIs in the industry allows for real-time monitoring thanks to the information feedback. This makes it possible to update them quickly and therefore facilitates the transmission of information between managers and the various employees.
What are the important digital indicators in the industry?
- Productivity
It can be analysed through the overall rate of return, the productivity rate but also the unused production capacity.
- Processes
They have a great influence on the operational efficiency, here we will analyse the average production cycle time…
- The delays
Here we are interested in the average time of a delivery, the average time of treatment of an order…
- Stock management
Here, we will analyse the amount of stocks, the rate of stock rotation…
- Resources
Here, we will check the reliability of the equipment, the average duration of equipment stoppages…
- Quality
It can be analysed via the rate of compliant products, the rate of defective products, etc.
What tools should be used to exploit the different digital indicators?
With the digital transformation, new tools and new management techniques have appeared. SESA SYSTEMS offers you tools that allow you to make the most of the data transmitted.
To analyse the various data during meetings, it is advisable to use connected devices such as the E-MEETING or the E-ACTIVBOARD. These are interactive, touch-sensitive screens that allow meetings to be conducted or information to be modified directly, particularly through digital KPIs.
It is important that all the KPIs are gathered in one place, SESAHUB is a software that allows to pilot the company with the different key performance indicators.
This type of software allows all employees to access the KPIs, via the automatic feedback of information that is provided by products such as the ANDON system.
How are the different KPIs managed?
Each department within a company has its own KPIs. The digitisation of performance indicators allows them to be transmitted in real time. This makes it possible to take potential problems into account more quickly, particularly in production. The digitalisation of KPIs helps to create or increase employee motivation because the changes made can be seen in real time, it also helps to improve processes and optimise the strategy in place.
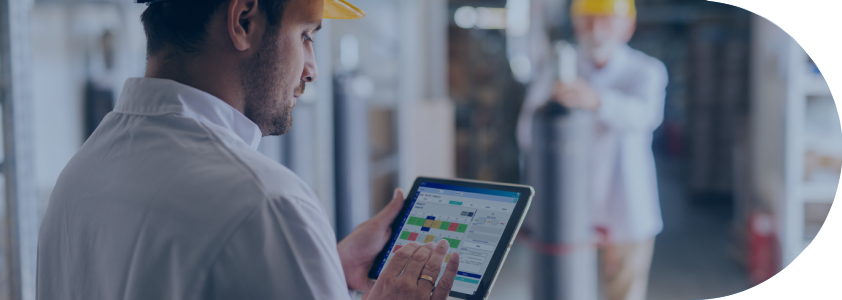
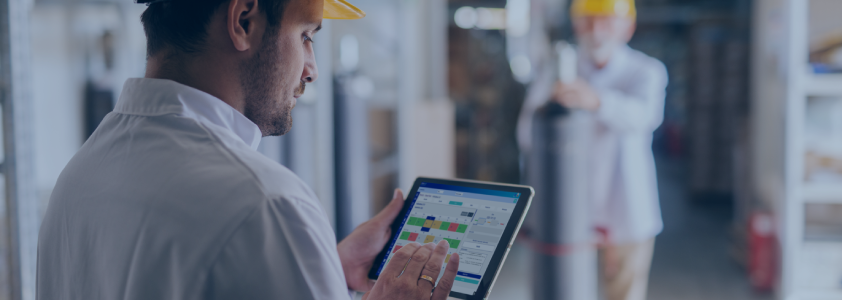